Solid carbide and indexable tools have their pros and cons. Choosing the correct tool for milling aluminum can be easy at times, such as using an end mill to finish the floor of a pocket or using an indexable face mill to deck off the top of a part. But then, there are applications where choosing a tool can become more complicated because of the different CAM software + machine tool capabilities. A large determining factor when deciding what tool to use for a roughing strategy is how much metal you can remove or your “material removal rate”. Material removal can be quantified by using the following formula:
Material Removal Rate (M.R.R.) = (Radial Depth Of Cut) x (Axial Depth Of Cut) x (Feed Rate)
So if we machined a piece of aluminum, assuming all factors except the tool parameters are the same, with a five flute 1/2" solid carbide end mill and a two flute 1.0" indexable end mill, we can see that the metal removed with the indexable tool is over twice that achieved by the solid carbide tool:
Diameter | IPT | RPM | # Of Teeth |
Inches Per Minute |
DOC | Radial Engagement |
Cubic Inches Per Minute |
0.5" | 0.005" | 7600 | 5 | 190.0 | 1.0" | 0.025" | 4.750 |
1.0" | 0.007" | 3800 | 2 | 53.2 | 0.6" | 0.350" | 11.172 |
the numbers tell us that size matters for milling aluminum
So, for roughing applications, we want to use the largest possible cutter that the application or machine tool will allow without chattering or stalling. This is one of the reasons why the machine tool is so critical! Large taper spindles with secure mounting such as dual contact are great for taking larger radial and axial depth of cuts without creating chatter. Small tools with a large radial and axial depth of cut may create chatter, limiting the engagement of the tool. Part designs also may be complex and CAM programs would only engage a cutting tool for a minimal amount of time.
When should you consider an indexable milling cutter vs. a solid carbide Tool?
This has many variables and while each situation should be assessed on a case by case basis, there are two factors that come to mind when deciding when to use an indexable tool over a solid carbide tool – price and reliability. The replacement cost of a solid carbide tool over the 1/2"-5/8" range can start getting expensive. Indexable tooling should start being considered at this point. While indexable tooling starts at diameters as little as 3/8", you may not always see the cost benefits on diameters this small. Cutting diameter sizes starting somewhere in the range of 5/8"-3/4" is where you start seeing good financial benefit.
The initial dollar value, however, may not be your determining factor. Process reliability such as chip management, tool changes, or taking advantage of a more reliable (sturdy) set-up may outweigh the benefits of aforementioned cost savings. Solid carbide end mills can create small, difficult to manage chips that can get into areas such as way covers, causing damage or requiring additional maintenance time. However, chips created with indexable tooling (due to the feed rate and depth of cuts) tend to be heavier and more manageable. Tool changes can be a determining factor as well. Although aluminum tooling with advanced coatings tend to have exceptional tool life, the ability to change insert corners after a certain lot or quantity for process reliability may also be a determining factor. Indexable tooling also offers multiple radii, coatings or substrates (such as PCD) to potentially add value to your application.
Here are some pros and cons on solid carbide and indexable tooling, to help you weigh your decision:
Solid Carbide Tooling |
Solid Carbide Tooling |
Indexable Tooling |
Indexable Tooling |
Precise. These high quality end mills are ground to the tightest tolerances and can be reground. |
Brittle. If you crash or chip, you may have to replace the whole end mill, limitation to regrinding. |
Most inserts come ground. |
Holder tolerances are generally looser. |
Can produce superior finishes. |
Limited feed rate capability. |
Can incorporate PCD inserts for mirror-like finishes. |
PCD inserts can be costly. |
Available in small diameters. |
Larger sizes are limited. |
Available in larger diameters. |
Smaller sizes are limited. |
Relatively low replacement cost on smaller diameters. |
Larger diameters can be more expensive. |
Replacement inserts are substantially less costly, and inserts can be indexed to get multiple cutting edges from each insert. |
Initial cost can be more expensive – some inserts are only sold in package quantities. |
Less pressure on tool. |
Setting up tools with minimal runout can be time consuming or costly. |
Can take more load and interruption. |
Higher tool pressure. |
Capable of deeper depths of cut. |
Can create small unmanageable chips. |
Capable of higher feed rates and creates thicker more manageable chips. |
Requires more power to run. |
WAnt to learn more About Aluminum machining?
We believe the Right Tool Is Everything™, and we strive to share our experience and expertise in an effort to ensure you select the right tool for your application and follow best practices. Download our Aluminum Machining Guide for invaluable information that will improve productivity and efficiency when milling aluminum.
You'll find information on:
- Insert geometries & shapes
- Insert relief angles, rake angles & approach angles
- AK special chipbreaker for aluminum
- Insert substrates, coatings & post treatment
- Troubleshooting insert failure
- Pros & cons of solid carbide vs. indexable tooling
- How to choose the right tool for your aluminum milling application
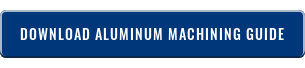