Watch this video to learn how to use a reamer to properly and efficiently ream a hole! Tech Team Expert Kurt Repsher walks you through the do's and don't's of reaming a hole with a hand reamer from planning to execution. Subscribe to our YouTube Channel to see more how-to application videos like this one!
What is a reamer & what is reaming?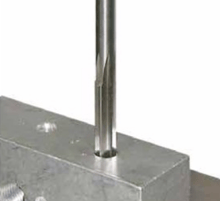
Reamers are multi-fluted cutting tools used to enlarge existing holes to a precise diameter. They are available in a variety of shank styles that can be mounted into hand tools, chucks, collets, or other tool holders, and are used in a variety of portable or stationary machines such as drill presses, lathes, screw machines, milling machines and more. The cutting end is ground with a 45° chamfer angle for easy entry into the hole. Straight fluted reamers are best for through holes, left-hand spiral flute models are better in blind hole applications. Available in a variety of materials, to suit the application and workpiece material, and some are available in almost any size imaginable. Light cutting oil or coolant is recommended for reaming operations.
HOW DOES A REAMER WORK?
A reamer is a cutting tool that is used to open the size of an existing hole by a small amount. A reamer will leave a smoother finish and a more precise size than a drill. Hand reaming, or reaming a hole without coolant or oil will result in an oversized hole and a rougher finish. Avoid reaming to the bottom of a blind hole.
What size drill should I use with a reamer?
- For reamers up to a 1/2": subtract 2% to 4% from the reamer diameter to determine the best drill size.
- For reamers 1/2" and larger: subtract 1/64” from the reamer diameter to determine the best drill size
how To use a reamer, step by step:
For the best reaming results, prepare your holes with just the right amount of stock for the reamer to remove. Too little, and the reamer will rub, leaving a smaller diameter than expected. Too much and the hole may be oversized and have a rough finish. Since reaming is about precision, use stub length tools where possible. The following is an example of how to ream a hole in metal. In this example, we are reaming a 5/16" (.3125") hole in soft, mild steel, step by step:
Step 1: Ensure that the workpiece is held securely and will not slide or rock.
Step 2: Locate & spot drill hole using a spot drill with a slightly greater taper than the drill being used. (For best results, avoid using a center drill (combination drill & countersink.)
Step 3:. Subtract 3% (since we’re working in mild steel) from the reamer diameter to determine the best drill size. (For example, .3125 – 3% = .3031"). A good rule of thumb to find the best drill size is to subtract 2% to 4% from the reamer size. 2% for harder metals, and 4% for softer materials.
Step 4: Use the appropriate drilling feed and speed for the tool, material and operation.
Step 5: Keep the drill and hole well lubricated with cutting oil or coolant.
Step 6: Drill the hole with a size N drill (0.302”). Peck drill to prevent chips from jamming and scoring the walls of the hole.
Step 7: Reduce the feed and speed:
RPM: Use 1/2 to 2/3 the speed of the drill that was used.
FEED: Double the feed of the drill that was used.
Step 8: Chamfer top of hole (just to break the edge) with either a 90° or 82° countersink.
Step 9: Since reaming doesn’t require heavy cutting fluids for optimal performance, use lighter oil or coolant. This will help to produce an accurate size hole and a smooth Finnish.
Step 10: Ream hole with a 5/16” reamer. Don’t stop or peck with the reamer until it exits through the bottom of the hole. With the machine turned off and the spindle completely stopped, pull the reamer straight up, out of the hole.
REAMING RECOMMENDATIONS:
- Workpiece hardness and machinability must be considered when setting machine speed and feed rate. Both play an important part in the life expectancy of a tool and the hole size and finish you wish to attain.
- If chatter is a problem, slow the cutting speed and increase your feed rate. Stock removal on reaming operations should not exceed 2% to 4% of tool diameter in most cases.
- Cutting oil or coolant is recommended for most reaming operations. Lighter oil and coolant will help to produce an accurate size hole and a smooth Finnish. Heavier, darker cutting oils might produce a slightly smaller hole size.
-
For the best reaming results, prepare your holes with just the right amount of stock left in them. Too little, and the reamer will rub, leaving you with more wear and less diameter than expected. Too much and you may have to repeat the process. A precise balance of stock in your holes will give your reamer the best surfaces for optimal performance.
-
After selecting the optimal reamer option for your materials, ensure that your pre-drilled holes are the correct diameter. Now you can set the correct speeds and feed for your application.
-
Keep your workpieces rigid, and ensure there is zero play in your spindle machine set-ups.
-
Using higher quality chucks to hold your straight shank reamer can help prevent slippage. Slippage during automatic feeder operation can cause damage and breakage to your reamers.
-
Reaming doesn’t require heavy cutting fluids for optimal performance, so utilizing soluble oils with 40-to-1 dilution should suffice for most applications. If dry machining gray iron, air blasting can improve your surface preparation results.
-
Check concentricity between your high-precision centers regularly, and regrind your bevel leads when necessary.
-
Keeping your reamers sharp can maintain accuracy and hole quality while improving tool life.
-
Make sure tool over hang from machine spindle is kept to absolute minimum.
-
Use a soft faced hammer if utilizing morse taper shank reamers.
-
Remember to check the flutes in your reamer for chip blockage throughout operation.
Popular types Of Reamers:
For a complete listing of all reamer types and styles, view or download our comprehensive Holemaking Guide, available via the link below.
Chucking Reamers, or “Machine Chucking Straight Shank Reamers” are used to enlarge existing holes to a very precise diameter. Chucking reamers have round, straight shanks which can be mounted in chucks, collets, or other tool holders, and are used in a variety of portable or stationary machines such as drill presses, lathes, screw machines, milling machines and more. Chucking Reamers are available in almost any size imaginable.
Taper Shank Chucking Reamers are like Machine Chucking Straight Shank Reamers, but these have a Morse Taper shank that will fit a same-size Morse Taper spindle, socket, or toolholder. They’re multi-fluted cutting tools, used to enlarge existing holes to a precise diameter. The shanks on these reamers are used in a Morse Taper spindle, socket, or toolholder.
Shell Reamers are also like Machine Chucking Straight Shank Reamers and Taper Shank Chucking Reamers but without a shank. They are used with a shell reamer arbor, which fits the hole in the reamer. Shell reamers are used to produce larger holes of 3/4" diameter or greater. Shanks/arbors are sold separately and will fit a range of Shell Reamer sizes, which makes these reamers an economical choice for your large-hole reaming needs.
Adjustable Blade Reamers are versatile reamers due to their broad size ranges and are used by hand for resizing of hole diameters to a precise size. The replicable blades slide within tapered slots in the reamer body by loosening the nut at one end and tightening the nut at the other end, allowing the reamer to maintain a specific size. Adjustable Blade Reamers are recommended for through-hole operations.
Want to learn more?
We believe the Right Tool Is Everything™, and we strive to share our experience and expertise in an effort to ensure you select the right tool for your application, follow best practices, and can push your productivity further.
Download our Holemaking Guide by clicking below. By downloading, you'll learn about:
- Drill style, length and shank options and when to use them
- Choosing the right drill for your material with included drill selection chart
- Drill performance levels
- The benefits of coolant-fed drills
- Reamer types & when to use them
- Speed & feed recommendations for reamers
- Troubleshooting counterboring applications, and more!