Perform Regular, Preventative Maintenance
Preventive maintenance can help prolong the life of your machines, reduce downtime, and increase productivity, and ultimately, bring down the cost of daily operations. Some of the preventive maintenance recommendations include:
-
Create regular inspection schedules and document findings to ensure your machinery and equipment are regularly maintained and anything out of the norm can quickly be identified. Use the records of tests and maintenance observation forms as a source of information that can be used for predictive failure analysis.
-
Change filters regularly to avoid contamination from potentially damaging chips or tramp oil in your coolant.
-
Perform regular maintenance of your metalworking fluids and sump, troubleshoot your metalworking fluids, and always make sure cutting fluids and your sump are clean, especially during tool changes.
-
Use high quality tool holders like Technik's CoolBlast Balanced End Mill Holders or Accutek's ER Floating Collet Chucks, as you do truly get what you pay for. Poor quality tool holders are more likely to have more TIR, which shortens tool life and reduces the workpiece finish quality.
-
Avoid using corroded, rusty, worn or damaged tool holders, as any distortion is transferred to the spindle. Replace damaged tool holders immediately.
-
Routinely inspect of the O-ring or seal located at the toolholder/coolant tube interface on machines with a coolant-thru spindle to avoid contamination of the spindle cartridge.
-
Ensure proper spindle lubrication to avoid chatter, friction, and potential overheating.
-
Keep the water trap on a machine's compressed air regulator clean to avoid particulate contaminants from being released and impacting critical components like spindle bearings.
Avoid Crashes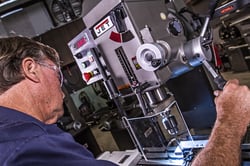
A collision of the spindle with the workpiece or the machine tool components often causes downtime. Whether caused by a misaligned tool, a programming error, or human error, the result is typically a costly spindle repair, scrapping the workpiece, broken tooling and damaged tool holders and even machine components. Steps to avoid the potential for a collision or crash at the spindle include:
-
Stay within the load, speed, and feed parameters recommended for each individual operation. Refer to our aluminum milling speed & feed guide for vendor-specific recommendations.
-
Recognize that any crash can be severe. A serious collision will often result in obvious, visible damage, but even a 'small' or relatively minor crash should be taken seriously. Even 'small' mishaps can result in dents or the wear of bearing surfaces which can accelerate spindle degradation and impact spindle life and performance and workpiece quality.
-
Utilize “safe start” blocks of code, which prevent an operator from restarting a program in the wrong position.
-
To eliminate any uncertainty in a new program, perform a trial run before making any chips.
Listen To Your Machines!
A change in harmonics is often one of the first warning signs that something is going wrong. A tool, toolholder, and a spindle will vibrate naturally as they interact, but a change in the harmonics or vibration – a sudden increase in chatter or declination of surface finish – requires your immediate attention. It is important to reduce or eliminate chatter in machining to ensure you:
-
Prevent damage to dynamically moving parts of a machine including the gears, bearings, guide ways and spindle assembly that can be caused by persistent vibration.
-
Continue to stay within the load, speed, and feed parameters recommended for each individual operation. Refer to our aluminum milling speed & feed guide for vendor-specific recommendations.
-
Avoid exacerbating the results caused by excessive chatter, recognizing that machine programmers or operators most commonly identify and address the source of the vibration by modifying speeds and feeds, depth of cut, radial load, type of cutting tool, or by reprogramming a tool path, all of which can impact production rates.
ENSURE YOU'RE USING THE OPTIMAL SPEED & FEED, EVERY TIME
We've compiled aluminum milling speed and feed charts and recommendations from the most popular manufacturers and created a downloadable PDF guide that puts this invaluable reference at your fingertips. Remove the guesswork from your aluminum milling applications and approach each job using the optimal speed recommended to further reduce the risk of downtime or repair at the spindle.
Download your Aluminum Milling Speeds Guide and find aluminum milling recommendations from manufacturers including:
- AB Tools
- Korloy
- Promax
- Rushmore USA Tools
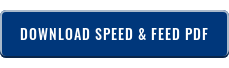